Packing powders: Practical considerations for handling particulates
Vertical form fill and seal (VFFS) packaging machines offer speed, accuracy and versatility. They can be adjusted to work effectively with a wide range of materials, including powders which have their own particular challenges, as Keith Marrow, our Applications Manager, explains.
Powder Properties
Salt, chemicals and spices are all very different, but all of these are classed as powders and handled as such. When specifying and customising a Vertical Form Fill and Seal machine, we consider the specific properties of the power. Different powders have different particle sizes, some larger than others. How does the powder handle? Will the powder flow freely, or is there a possibility it will stick or suffer from compaction issues?
We must also consider the powder and its properties; for example, is it corrosive? If it is, a painted steel packaging machine may eventually show its age, so a stainless steel vertical form fill and seal machine could be the better option.
As well as being more corrosion-resistant, a stainless steel finish will keep its clean appearance in the most challenging situations. However, the operating environment and budget may dictate which finish is required.
Handling
Different powders have different textures; some are easily handled, others are not. Some powders can be weighed others must be screw-fed by an auger. More often than not, coarse powders/granular products can be weighed.
Environment
Every factory or production plant is different. We need to think about the environment in which the machine will be working and how these conditions affect the powder. Most of our clients have already considered factors such as humidity, temperature and whether or not a high-care finish is required.
ATEX Considerations
Depending on the powder being packed, we may need to consider ATEX.
ATEX is the name commonly given to the two European Directives for controlling explosive atmospheres: Directive 99/92/EC (also known as ‘ATEX 137’ or the ‘ATEX Workplace Directive’) and Directive 2014/34/EU (also known as ‘ATEX 114’ or ‘the ATEX Equipment Directive’)
In Great Britain, Directive 99/92/EC requirements were enacted through regulations 7 and 11 of the Dangerous Substances and Explosive Atmospheres Regulations 2002 (DSEAR).
DSEAR requires employers to eliminate or control the risks from dangerous substances, such as combustible powders, such as sugar or flour.
Usually, when sugar or flour is handled, it is perfectly safe. So, if you had a small amount of either powder on a kitchen table and lit a match next to them, nothing would happen other than the match burning itself out. However, if there’s a large amount of sugar or flour and it’s airborne, inside a factory or production line, for instance, and then you light a match – both would explode!
Packaging
Customers usually come to us with fairly well-developed ideas about the type of packaging they want to see their product in. However, not all film types and bag styles are suitable for handling powders. Therefore close cooperation with our customers is GIC’s strong point.
Static
Another consideration is the build-up of static and how the powder is affected by it. The film type and the powder need to be able to resist or not create static, as this may well impact the seal quality and efficiency of the production line.
Down Stream Presentation
Depending on how the final packaged product will be packed, we may need to change its presentation to suit secondary or end-of-line packaging.
We work with a wide range of clients, some just starting to move towards automated packaging and others upgrading their machinery and knowing what they require. Irrespective of where you are on your journey, if you need help, advice or a quotation, please don’t hesitate to contact us by emailing info@gic.uk.net, calling 01472 611 885 or filling in our contact form.
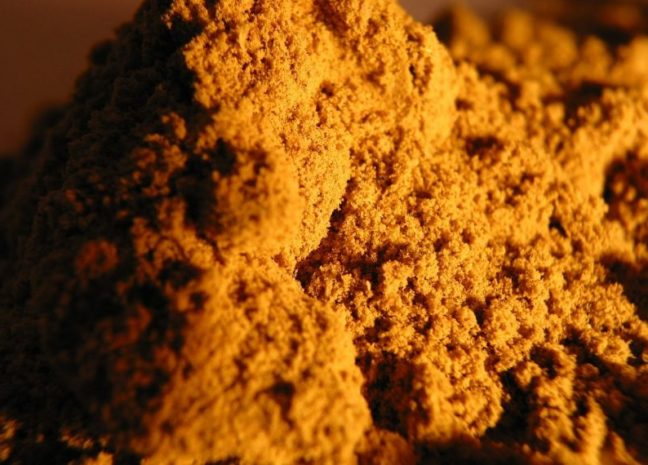