GIC introduces retrofittable leaf salad technology to increase packaging rates and reduce seal contamination
An innovative technique that increases the bagging speed of leaf salads and reduces both film use and contamination levels can now be fitted to already commissioned Vertical Form Fill and Seal machines.
Packaging machinery manufacturer, GIC, introduced its Leaf Salad Assisted Drop feature last year.
Leaf Salad Assisted Drop eliminates upstream choking by creating an area of low pressure in the product chute which draws salad leaves down into the bag in one single slug. Without the feature, the product mass often elongates into several clumps of salad leaf, which increases the chances of causing contamination by being captured in the seal.
As of November 2019, GIC has supplied 15 machines featuring Leaf Salad Assisted Drop. Companies, such as Intercrop, one of Europe’s foremost salad growers and a pioneer in the mechanisation of the salad harvesting process, have reported significant increases in productivity since using GIC’s machines.
Until now the Leaf Salad Assisted Drop technology could only be incorporated in new machines. However, following several months of development work, GIC’s engineers have developed a way to fit the feature to machines that are currently running.
“We think this is a potential game-changer,” says Andy Beal, managing director at GIC. “Salad producers are keen to reduce the amount of film they use, and they want to see fewer salad leaves sticking in the seal as it can cause contamination and downtime. They also want to increase bagging speeds. That’s why we developed Leaf Salad Assisted Drop machines. The range has attracted a lot of interest, and we’ve sold machines to some of Europe’s largest salad producers. Obviously, there are a lot of packaging machines in use, and while people have been bowled over by the new technology, they’re not in a position to buy brand new machines with it in. So, we tasked our design team with developing a way to retrofit the Leaf Salad Assisted Drop functionality to machines currently in use.”
The retrofit includes all the mechanical and electrical parts plus a software update. The process takes around 8 hours to complete and, based on reports from current users, delivers around a 10% increase in productivity, vastly reduced seal contamination levels and downtime.
Based in Gainsborough, Lincolnshire, GIC was established more than 30 years ago and employs 25 people. The company manufactures an extensive range of vertical bagmakers, producing a wide range of finished bag sizes from 150 to 600mm wide, in both intermittent and continuous motion variants. All GIC machines offer low-cost ownership, robustness, reliability and exceptional build quality.
GIC’s machines integrate seamlessly with ancillary equipment such as check-weighers, multi-head weighers, cup fillers and counters, with the company offering efficient and cost-effective after sales to all of its customers in fresh and frozen produce, cereals, snacks, confectionery, pasta, powders and pulses, industrial hardware and liquids.
For further information about GIC and its Leaf Salad Assisted Drop functionality, visit www.gic.uk.net, email info@gic.uk.net or call 01427 611885.
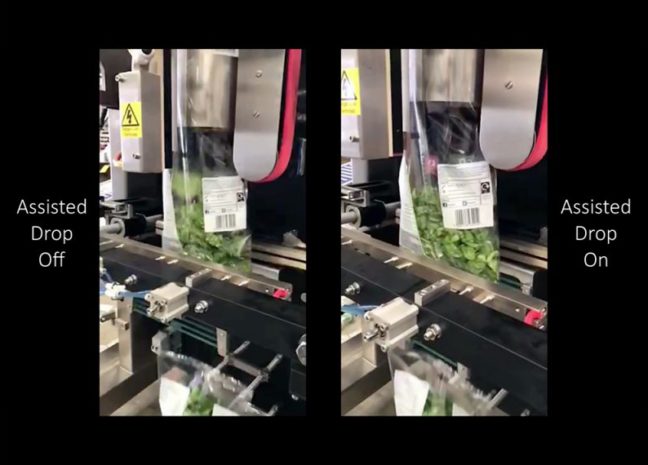