Going with the flow: Packing liquids with vertical form fill and seal machines
Vertical form fill and seal packaging machines are incredibly versatile, and while most GIC machines are found packing solids, they are equally as efficient packing liquids.
Today, as well as fresh and frozen produce, bullion and proteins, GIC machines, are handling sauces, marinades and various liquids with and without suspended products, such as ham, seeds and other particulates.
To the inexperienced, packing liquids can be a daunting prospect and a real challenge to get right. The speed of the transport cycle has to match the pump dosing, and the viscosity of the liquid can vary a lot, with some flowing more quickly than others. In our 36 years of designing and building vertical form fill and seal packaging machines, we have found that there is no ‘off the shelf’ solution for packing liquids. Every project needs a bespoke solution.
All our vertical form fill and seal packaging machines, from our smallest unit – the CUB – up to a GIC4100, can be optimised to pack liquids. Over the years, we have mastered designing flexible control systems that can handle pack volumes from 30ml to 12 litres.
When developing an effective vertical form fill and seal solution for liquids, the first challenge is understanding the product and its characteristics, including the temperature required at the point of packing. Then the bag needs to be made just at the right time in conjunction with the act of depositing. Contamination of the seal area is then to be avoided by the use of GIC control parameters.
Ensuring the pump operates in synergy with the bag forming is crucial. The liquid can splash onto the side of the pack if the pump is too fast. If the pump is too slow, valuable time will be lost and possibly lead to seal contamination. While we don’t design pumps, we do work very closely with pump manufacturers and have been known to project manage to ensure the optimum design and seamless integration with our vertical form fill and seal machines.
Perhaps our most challenging project was developing a machine to pack ten litres of Minestrone soup. We had a good starting point, having previously developed a vertical form fill and seal packaging machine that placed chicken pieces and a marinade into a 2kg pillow pack.
Our solution for adding the marinade and the chicken pieces into the same pack saw us insert an injector system down into the forming tube. As the chicken went down the tube, the marinade was also dispensed to coat the chicken pieces.
The soup project was also challenging, requiring a twin pump solution with full synchronisation and control from the GIC HMI. In most applications, our vertical form fill and seal machine talks to just one other component, a pump, weigher or auger. In this instance, our machine needed to talk to a twin servo pump. This presented us with hardware and software challenges, but we overcame them and even added variable delay features within the two pumps so that the operator had greater control over them. They could start the machine in either a single pump or twin pump configuration from the GIC product recipe page.
As well as working closely with pump and weigher manufacturers, we have occasionally worked with film manufacturers to find the right film specification for a customer. Several factors must be considered when deciding which type of film is best for the application, including sealability, puncture resistance, the ability to take the product’s weight when running a hot fill, and light infiltration. Most liquids are packaged in a laminate film, with nylon, PET or OPP on the outside and polyethylene on the inside.
Many liquids are packed in pillow packs, but at GIC, we have also developed a way to pack into a piping bag, which makes releasing the liquid incredibly easy and accurate – you just cut one corner off the trapezoidal pack and squeeze.
The final consideration for food manufacturers working with liquids is the ease of changing the forming set. Food manufacturers may require several forming sets, one for each pack width. As most companies working with liquids tend to do lots of short runs, of around two to three hours, they are changing the forming set regularly. As well as easy and quick removal and installation, GIC’s forming sets are available in stainless steel for hygiene and can be removed without using tools.
We work with a wide range of clients, some who are just starting to move towards automated packaging and others who are upgrading their machinery and know what they require. Irrespective of where you are on your journey, if you need help, advice or a quotation, please don’t hesitate to contact us by emailing info@gic.uk.net, calling 01472 611 885 or filling in our contact form.
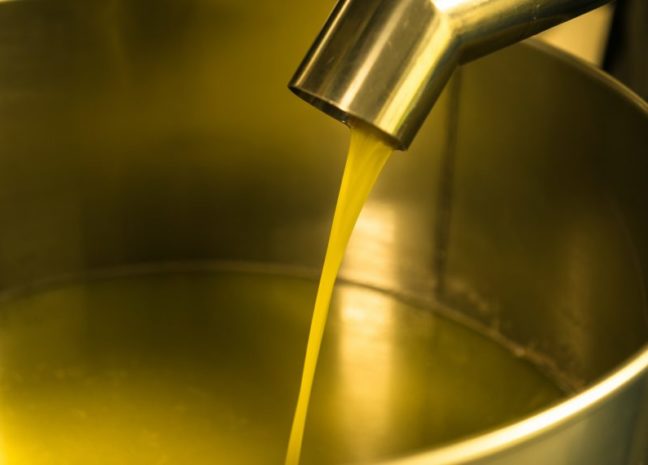